La parada programada del área Química que desde el pasado mes de mayo se está desarrollando en el Complejo Industrial de Repsol de Puertollano pasa por su ecuador. Entre los proyectos de inversión que se están llevando a cabo destacan los ejecutados en las plantas de Olefinas (petroquímica básica) y Polipropileno (una de las plantas del área de química derivada).
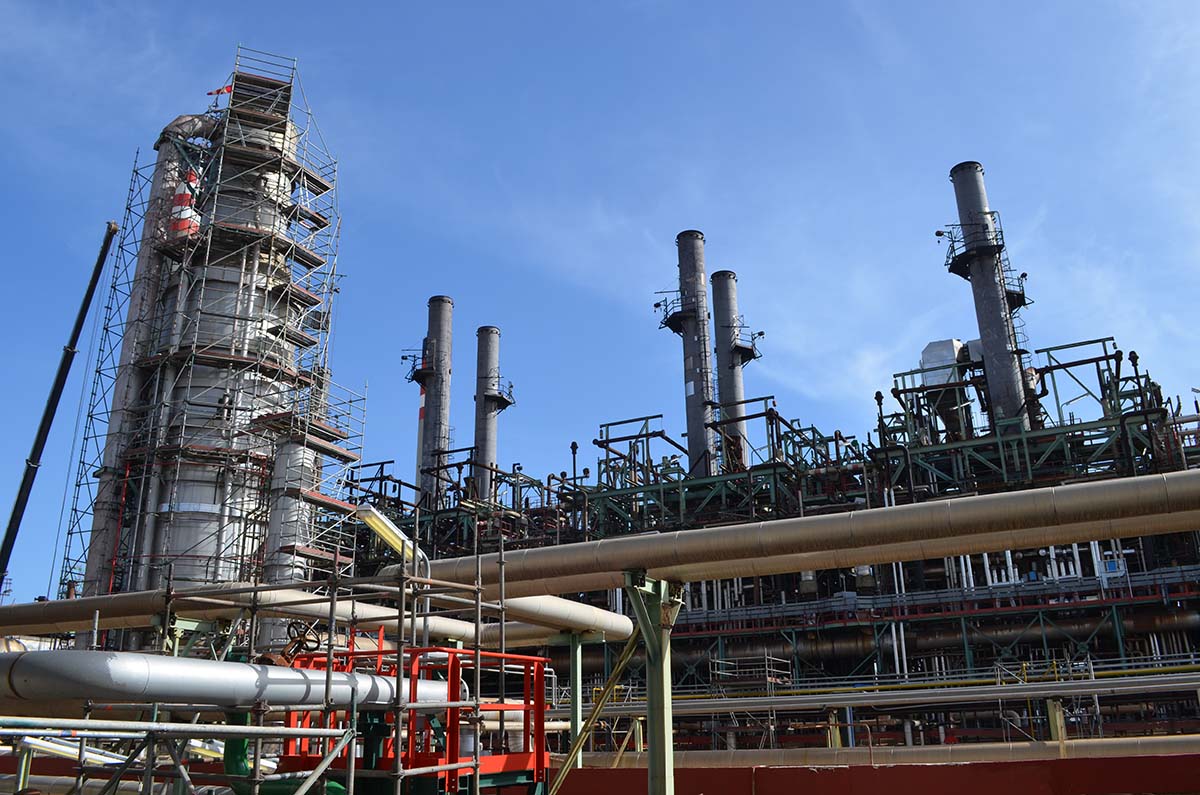
Estos proyectos, cuyo objetivo es incrementar la eficiencia energética, la competitividad de las instalaciones y la instalación de tecnologías que ayuden al a descarbonización se enmarcan dentro de la estrategia de Repsol de avanzar en la transformación industrial del Complejo Industrial de Puertollano con procesos más eficientes, impulsando tecnologías punteras e innovadoras y preparando las plantas para un nuevo ciclo productivo, según ha informado la compañía en nota de prensa.
Uno de los trabajos más significativos en este sentido ha sido la sustitución de la turbina de vapor que acciona el compresor principal de la planta de Olefinas por un motor eléctrico. Esta nueva inversión reducirá las emisiones de CO2 del Complejo Industrial en más de 68.000 toneladas al año y los costes energéticos de la planta en un 25%, disminuyendo los consumos de vapor de la unidad de Olefinas.
De esta forma se ha pasado de alimentar la planta con vapor a alimentarla con electricidad en una apuesta de la compañía por electrificar sus procesos industriales, reduciendo así la huella de carbono de su actividad. Para dotar de energía tanto el motor principal como los motores auxiliares de alta eficiencia, se ha construido una subestación eléctrica con una potencia instalada de 30 megavatios, capaz de abastecer de electricidad a una pequeña ciudad de 40.000 habitantes.
Para llevar a cabo la ejecución de este proyecto, se está contando con la experiencia y la capacitación técnica de empresas auxiliares, muy especializadas, la mayoría de la comarca de Puertollano. Además de las maniobras singulares que se han llevado a cabo como la extracción de la turbina y posterior instalación del motor con grúas de gran tonelaje y altura, se están llevando a cabo trabajos de inspección, mantenimiento y mejora de la unidad.
Julia Cortecero, coordinadora de la parada en el área de Petroquímica Básica, explica que “se está dotando a la planta de mayor robustez a la seguridad de la unidad con la instalación de nuevos sistemas de seguridad y mejora en los sistemas de antorcha”. Solo en esta planta, asegura, se están inspeccionando 200 equipos y “se están llevando a cabo más de 500 trabajos, en total más de 200.000 horas de trabajo a lo largo de estas semanas”.
Más competitivos y especializados
La planta de Polipropileno, una de las plantas del área de Química Derivada donde se produce polipropileno destinado fundamentalmente al sector de higiene y alimentación, es otro de los escenarios de esta parada.
Allí el proyecto se centra en optimizar la producción de la unidad, eliminando ‘cuellos de botella’ en el proceso con el fin de aprovechar al máximo su capacidad de producción. Se trata de uno de los proyectos de mayor alcance realizados nunca en esta unidad y que va a servir para adecuar la planta al esquema de producción integrado del Complejo Industrial, lo que supondrá, ampliar la producción de algunos grados y avanzar en la especialización del área Química.
De manera paralela, se ha construido e instalado una nueva antorcha con un doble objetivo: reforzar al máximo la seguridad de las instalaciones y minimizar el impacto medioambiental de la unidad e incrementar la capacidad de la antorcha para dar servicio a nuevas plantas. La nueva antorcha tiene 100 metros de altura y se lleva trabajando en ella desde el pasado mes de octubre.
Francisco González Funez, coordinador del área de Química Derivada en la parada asegura que “estos dos proyectos se han estado ejecutando con la planta en servicio durante el último año, lo cual ha supuesto un esfuerzo importante de supervisión y coordinación con la actividad propia de la unidad”. Entre otros trabajos, el proyecto se ha completado con el montaje de seis nuevos silos con una estructura de 250 toneladas.
En el resto de unidades del área de Química Derivada, como Polioles/Butadieno y Polietileno de Baja Densidad (PEBD/EVA), se están desarrollando proyectos enfocados a incrementar la fiabilidad y competitividad de las instalaciones y realizar mejoras en seguridad.
En total, Repsol va a invertir más de 107 millones de euros en esta parada del área Química con el objetivo de avanzar en los objetivos marcados dentro del Plan Estratégico 2021-2025 de la compañía, centrados en transformar sus centros industriales en hubs multienergéticos capaces de generar productos de baja, nula o incluso negativa huella de carbono y llegar a ser una compañía cero emisiones netas en 2050.